The manufacturing industry is one of the largest employers in India. More than 22 million workers are employed by manufacturing businesses. With such a large workforce, delegating work and keeping operations smooth would be easier. But, the manufacturing sector in the country suffers due to overtime issues.
Overtime in the manufacturing industry is a problem for companies and workers. Once overtime was seen as a way to improve productivity, but now it is considered one of the most significant stress sources that lead to poor work-life balance.
This article will discuss how to reduce overtime in manufacturing without affecting output. We will list some strategies to overcome the issue.
But first, let’s find out why overtime can be counterproductive.
Why should organizations try to reduce overtime?
Overtime is the number of hours employees work that exceed their regular hours. Companies and HR managers often overlook the dangers of overtime. But, when observed closely, it is startling how costly overtime issues can be. Not only can it adversely affect the company’s bottom line, but it can have side effects on the workers.
1. Financial Impact
The financial burden for the company to compensate overtime can be a significant undertaking. According to the labor laws in the country, employees must be remunerated at twice the rate of their regular working hours. While some employees might need to work overtime for extra income, others use overtime rates to work unnecessarily to be compensated above their average wage rate.
For a company paying employees overtime rates for work that can be accommodated during the regular shift hour is a pitfall that can profoundly affect its bottom line.
2. Impact on performance
A more visceral effect of overtime on workers is the reduced performance. In this whitepaper, J. Nevison clearly illustrates that over time can negatively affect performance. He suggests that there is little productive work done when workers need to work over and above 50 hours per week.
Two other supporting studies found the whitepaper valid and showed that workforce productivity drops by an additional 10 hours with an increase of 4 to 12 hours in their work shifts. Overworked employees are less focused on their jobs and feel alienated in the workplace. It also has an impact on their morale making them more susceptible to performance issues.
Companies must be aware of the financial liability of such a decline in productivity.
3. Precursor of health problems
While financial and productivity impacts can be managed, the harmful effects of overtime on workers’ health are even more severe. Countless studies link overtime or overwork to health issues. It leads to poor work-life balance that also affects personal relationships.
According to one study, workers who worked three or more hours longer than the usual shift (7 hours a day) are at a 60% higher risk of heart and cardiovascular health issues. Other health issues are associated with overtime, such as high blood pressure, increased stress, anxiety, lower back problems, alcoholism, and addiction issues.
All these issues bring productivity lapses in the workforce, leading to higher absenteeism rates.
6 Ways to reduce overtime in the manufacturing industry
When you identify the causes of overtime in your company, it is essential to resolve them as soon as possible. Furthermore, if your company doesn’t experience regular overtime hours, you should still have measures to avoid overtime.
Here are some ways using which manufacturing companies can reduce overtime.
1. Make sure your team has the right tool, equipment, and resources to complete the work on time
To reduce overtime, you have to make all the right tools and resources available that allow the most efficient use of employee hours. Allow workers to work smarter, not longer. There are a lot many manual and administrative tasks that can be automated to free human resources.
People working behind the desk often spend more than one-fourth of their day reading and responding to emails alone. How can you expect to reduce overtime if the monotonous, day-to-day task consumes a quarter of workers’ shift time? It is why it is necessary to automate such tasks to allow workers to focus on more productive tasks that add value to the company and boost productivity.
You can use tools like Asana and Jira for project planning and team collaboration. Manual attendance keeping and leave management is one task that takes much time for the HR team to manage. With the availability of attendance systems like Truein, recording and managing attendance can be automated.
It has several benefits for both employees and HR managers. Truein integrates with payroll software, so it is easy to track attendance and overtime to pay only for the hours a worker worked. As an automated face-recognition system, workers cannot trick Truein with time theft.
These are little adjustments at the outset but can go a long way to reduce overtime. When you free up human resources, they invest most of their time on actual responsibilities.
2. Create an overtime policy
Just verbal overtime instructions will not help curb overtime. It would be best if you had a well-thought overtime policy to communicate company expectations to the workers. An official overtime policy explains all the aspects of working overtime. It details how employees will be compensated for overtime hours.
Discuss with the HR managers how to reduce overtime in manufacturing by implementing an overtime policy. When preparing the overtime policy, clarify who will approve the overtime hours, manage shifts, and how much say the employees have in the matter.
For a detailed guide on how to create an overtime policy, check out this post. Just creating an overtime policy won’t be enough; you must ensure that all employees and managers have access to the overtime policy. Truein can help with it as well. HR managers can create and implement overtime policy from the dashboard, and employees can access the procedure on their smartphones.
Schedule a free demo today and see how Truein can help you to automate the attendance capturing and overtime calculation in your manufacturing industry.
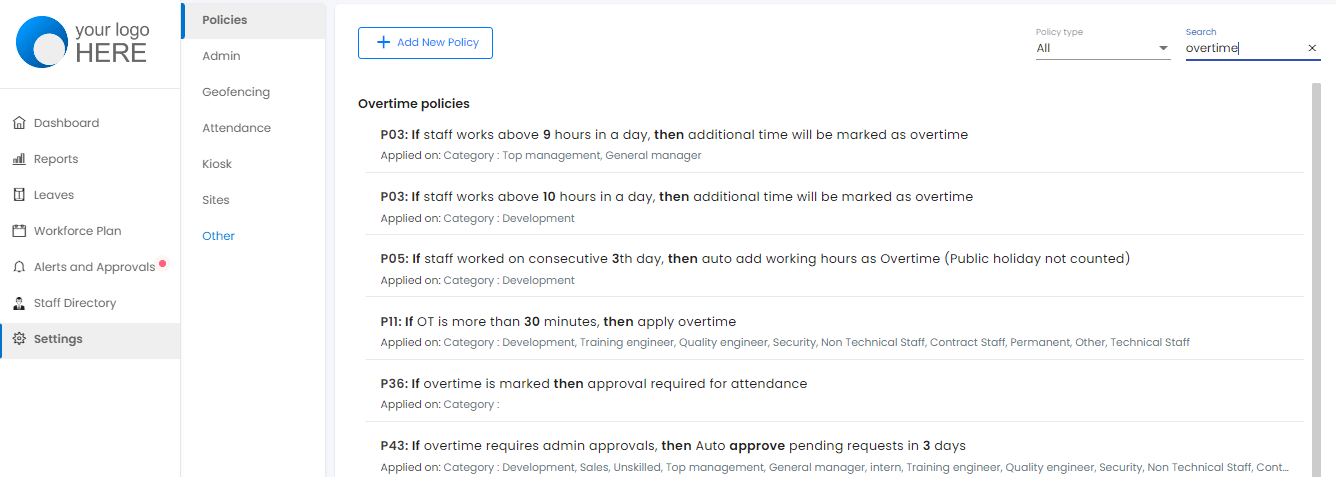
An official overtime policy leaves little scope for misunderstanding and lays strict ground rules for employees. It ensures workers are not exploiting overtime.
3. Cross-train your employees
In the manufacturing industry, it is possible to cross-train employees. For instance, having all the floor workers trained in handling CNC machines can save you money. Rather than scheduling overtime or hiring additional staff, you can pull workers from other departments to work on CNC machines during busy periods.
Cross-training employees can significantly benefit your company’s bottom line. It helps make schedules much more efficient and ensures workers are not working excessive overtime. You have to ensure there is no staff shortage in a department; if there is, cross-train other workers to pick up the slack instead of staff working overtime.
4. Allow flexible work schedules
It is a myth that the 9-5 work hours are the best for productivity. Many workers report that working from home is more productive than working in an office. For the manufacturing industry, it is a challenge as most of the workforce needs to be present on-site to keep the production optimal.
While the administrative staff, to an extent, can be allowed to work from home, most of the workers need to be present in the office. You can have more flexible work schedules for workers to enable them to work shifts that are adjusted to the most productive hours.
Employees with flexible schedules can focus more, improving their productivity and reducing the chances of overtime.
5. Allow overtime only when required
While there are rules on how workers must get compensation for the overtime hours, there is no cap on how many hours employees can work for overtime. You must have policies that explicitly explain how many hours an employee can work overtime. As an employer, you have the authority to set overtime rules freely.
It would help if you allowed overtime only when it is required. Determine a weekly, monthly, or annual cap of overtime hours your business can afford. This will help you decide the scope of overtime employees can work when needed, ensuring that it does not become a norm.
It will also help distribute work evenly amongst workers such that all employees have an equal chance of working overtime hours for extra pay.
6. Schedule shifts
Employee shift scheduling must help to reduce overtime, not increase it. It is essential to ensure that your HR team is preparing employee schedules that are organized, managed, and updated regularly. It will allow your organization to accurately match staffing levels to the work demand and eliminate any requirement for overtime.
Truein can help you organize staff according to the need to distribute work and make schedules that accommodate work demands without overtime. If your company still relies on manual sheets or Excel to manage shifts and overtime, you will benefit by switching to Truein, which completely automates scheduling and attendance management.
It allows managers and supervisors to keep track of employees to ensure they are working their shifts.