In the manufacturing industry, productivity is directly correlated with revenue. It is essential to keep the productivity in manufacturing high because it affects costs and profitability and is critical to remain competitive. You should take all the necessary steps to get a competitive edge.
This article will entail tips on how to increase productivity in manufacturing, but before that, let’s find out how manufacturing productivity is calculated.
How to calculate productivity in manufacturing industry
Manufacturing productivity is the simple ratio of output to input. It is a simple calculation of how much throughput or quantity you produce compared to the amount of input. The input of a manufacturing company includes labor, overtime, capital resources, natural resources, and other costs. The output is simply the number of goods produced.
You can calculate manufacturing productivity as follows:
Manufacturing productivity = Output / Input
For instance, if your company produces $10,000,000 worth of products in a month by employees putting in 5,000 hours, your company’s manufacturing productivity will be:
Manufacturing productivity = 10,000,000 / 5,000 hours = $2,000/hour.
However, this value does not equal profit as you have to consider wages, overheads, and other costs. We have kept the calculation simple to be able to understand the productivity level of the company. To truly improve manufacturing productivity, you must consider the following tips.
Six ways to improve productivity & efficiency in manufacturing
1. Check what problem your workers are facing
The workers are at the center of manufacturing productivity, and project managers should begin by assessing the workforce. You need to understand the problems workers are facing that are reducing their productivity. First, you have to establish that you have the right people working in the teams so that they can properly utilize the available resources and tools.
Next, evaluate existing workflow processes to determine how they can be improved. If there are any roadblocks in the process, ask for feedback from workers so you can plan a remedy. Also, you should explore the available technologies and equipment that can help workers improve their productivity with minimum effort.
These changes will affect manufacturing productivity positively. You can also have regular discussions with workers on improving manufacturing productivity. Workers on the floor handling machinery and equipment know better what’s not working. To enhance productivity in the long term, it is essential to engage workers during the planning phase.
2. Train your employees
If you find that workers lack essential skills, then it is vital to invest in training employees. Companies can improve manufacturing efficiency by implementing a training program to ensure proper coordination of workers and processes.
Industry experts agree that employee training is the cornerstone of every productivity strategy. Manufacturing companies should prioritize regular training and maintain detailed training logs of workers. To improve employee efficiency, as a manager, you can set up a personalized schedule for employees to track their progress over time.
If you install any new equipment, plan for dedicated training of employees. You should provide employees with additional industry resources and online tools that allow them to learn independently. This is important to set up a team that’s proactively learning to improve efficiency and problem-solving capabilities. A manufacturing industry survey found that a 10% increase in workforce education leads to a productivity boost of 8.6%.
3. Increase communication within and outside the company
Improvement of manufacturing productivity also depends on how efficient the communication is with the workers, key suppliers, vendors, and partners. The supply chain is an intricate part of the manufacturing process, so collaboration with suppliers and customer response time should be fast.
You can use several tools to improve communication within and outside the company. An ERP can help you maintain open communication with all the stakeholders by offering a constant flow of real-time data. You can track and monitor workers’ performance, supply chains, and operations.
With an ERP, you can watch the entire process from procurement to production to distribution which will help you make better decisions. When all the data is available within your dashboard, you can quickly identify shortages or performance issues hindering manufacturing productivity.
4. Maintain the machines properly
If your organization is not regularly inspecting tools for efficiency, productivity may lapse. It is surprising to see how many managers look for ways to improve operational efficiency in manufacturing violence while neglecting the machines’ essential maintenance.
In manufacturing, this is considered a cardinal sin. We understand that maintenance schedules are inconvenient as they cost time and money, but in the long term, they are an essential part of keeping operations active and equipment safe for workers. Also, companies should keep exploring new and better tools for the job to improve productivity without increasing work hours.
Train your staff to keep an eye out for what’s happening with each machine. Maintenance schedules should be consistently maintained. And you should keep spare parts, cables, and other components available for immediate replacement if things break down. Time lost due to breakdowns is one of the main contributors to reduced manufacturing productivity.
5. Schedule shifts of employees
Shift scheduling in manufacturing can improve productivity by ensuring that the correct number of workers are on hand to handle the workload at any given time. This can reduce workers’ idle time, which can increase overall efficiency and productivity. Additionally, well-designed shift schedules can help reduce absenteeism and turnover, which can also positively impact productivity. Advanced scheduling software like Truein can make it easier to create and manage shift schedules, further improving efficiency.
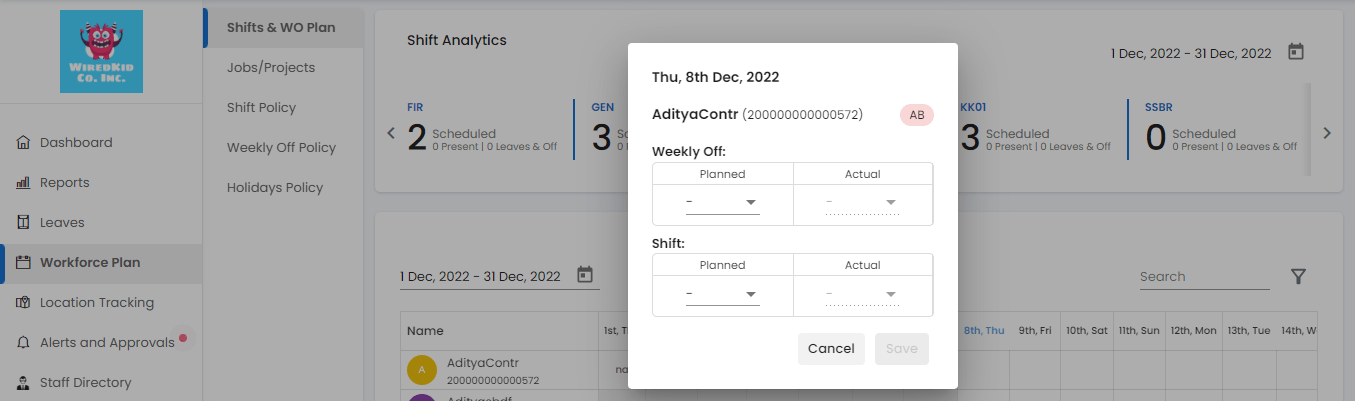
Schedule a free demo today and see how easily you can schedule shifts from the Truein app and web dashboard.
6. Automate the manufacturing process
Automation has been helping manufacturing industries for decades to improve productivity. However, in the 21st century, automation is more than just utilizing CNC machines. Today automation means diving deeper at the process level and automating tasks that can reduce time spent on managing processes by boosting productivity.
For instance, employee time and attendance management can be easily automated with software like Truein. It is a cloud-based, hardware-less workforce attendance management system that can be easily deployed in the manufacturing industry. It helps managers track employees in real-time and monitors important metrics like attendance, overtime, leaves, location, etc.
Schedule a demo and see how you can collect all the employee data that can help you to learn about the productivity of individual employees and then you can take the necessary actions required to boost productivity.
Also, ERP software can be used to automate workflows such as inventory management, vendor communication, and report generation.